Bhupendra Khandelwal
Associate Professor
http://bkhandelwal.people.ua.edu
https://scholar.google.com/citations?hl=en&user=JDlPHmQAAAAJ
https://www.linkedin.com/in/bhupendra-khandelwal-7773b713
Students:
Seyed Amin Ghorashi, Jerry Hamilton, Mahdi Jahami, Vamsi Krishna Undavalli, Chuming Wei
This lab focuses on sustainable fuels including sustainable aviation fuels (SAFs). Our work involves evaluation of fuels and its components on thermal stability, fuel supply systems, combustion, emissions, and engine performance.
Thermal Stability Fuel stability is affected by exposure to heat which can be difficult to quantify. We have developed a test apparatus to quantify the effects of heat exposure on the stability of the fuels, with a particular
emphasis on understanding how heat exposure times and temperatures influence fuel behavior.
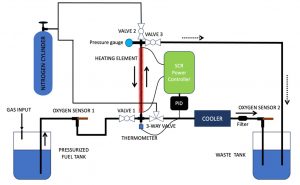
In the setup, various gases are used to pressurize the fuel tank based on the specific demands of the test, delivering the fuel into the system. The precise regulation of the fuel’s temperature is achieved using a heating element, controlled by a Silicon Controlled Rectifier (SCR) power controller employing PID feedback system to adjust the applied heat based on real-time temperature data collected by a temperature sensor. The system’s configuration includes valves to ensure that the fuel is appropriately confined within the heating zone for the desired duration.
Thermal stability test rig could be used to evaluate current liquid fuels and develop future liquid fuels. With increasing engine temperatures, this test set-up is expected to provide knowledge to custom design fuels that can sustain exposure to high temperature environment upstream of the combustor.
Elastomers/Seals Elastomer Dynamic Compression (EDC) System was developed to measure the changes in internal forces of O-ring elastomers while subjected to flowing fuel. The system includes a materials test rig, force compression measurement rig, and various special tools required for operation. The materials test rig is composed of fuel storage, fuel pump, O-ring mount plate, compression plate, load cells, electronics housings, DC power supply, and stand. Additionally, the test rig contains various sensors including a fuel temperature probe, fuel pressure transducer, ambient temperature and humidity sensor, and four highly sensitive load cells.
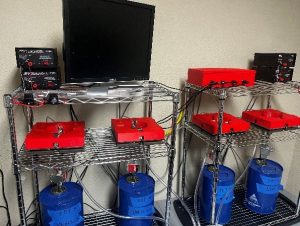
Ease of operation of the test rig was at the forefront of the design process. Setup of each experiment consists of cleaning, replacing test specimens, and application of compression forces. Each experiment can be remotely monitored with data analyzed in real time. The average length of each experiment lasts for 500 hours. The application of EDC system is to evaluate fuel systems compatibility for current and future fuels, while also assisting development of better elastomers for SAFs and other sustainable fuels.
Combustion & Emissions A modular combustor test bench using the Rolls-Royce Spey combustor has been developed. Alternative fuel blends can be readily tested to comprehend the combustion process in isolation. The fuel flow is regulated through a Coriolis flow meter, and a high-pressure line supplies about 0.1 kg/sec of air flow rate; higher airflow rates up to 1 kg/s are feasible with modification. The fuel injection system is modified to evaluate and understand the multiphase multifuel combustion for various alternative fuel blends and their influence on extending fuel flexibility capabilities for gas turbines.
The bench offers optical access into the flame zone and capabilities to measure emissions. It is equipped with multiple thermocouples to measure the liner temperatures and allows operation at maximum combustion temperatures of about 2000 °C. An integrated Data Acquisition (DAQ) system built on LabView allows the operator to analyze all the measurements during combustion from a single, centralized location.
The lab also houses two state-of-the-art gas turbine units: the Honeywell GTCP30, an Auxiliary Power Unit (APU), and a Rolls-Royce Gem turboshaft engine, which powered the military helicopter Westland Lynx by Augusta Westland.
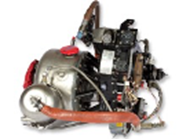
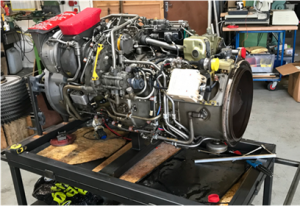
Wood Heater Working with Industrial Combustion lab, we are improving the thermal efficiency of wood fired heaters by refining the heat extraction methods such that the exhaust temperature of flue gases is minimized. Extended surfaces both inside and outside the heat transfer box around the wood combustor provide efficient heat removal as shown in the figure. CFD analysis based on ANSYS FLUENT is used to guide the design of extended heat transfer surfaces while considering factors such as overall weight, cost, maintenance, and durability.
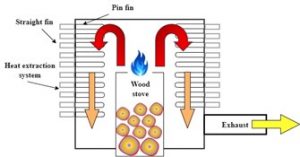
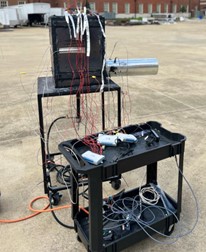
Electrical power is required to operate the fans, sensors, and control system. A thermoelectric generator (TEG) is employed to convert a portion of the heat directly into electrical energy, enabling the wood heater to operate independently from the grid. The TEG system takes advantage of the high product gas temperatures to generate electricity, which is stored in a battery with a smart converter for efficient charging and power distribution. We plan to minimize electrical power consumption and thermally integrate TEGs to provide high conversion efficiency.
Research Examples:
Related Publications:
- B Khandelwal, “Aviation Fuel” Aviation fuels First Edition, Academic Press Elsevier, ISBN: 9780128183144.
- V Undavalli, OBG Olatunde, R Boylu, C Wei, J Haeker, J Hamilton, B Khandelwal, “Recent advancements in sustainable aviation fuels”, Progress in Aerospace Sciences 136, 100876, (2023).
- J Hamilton, K Elliott, P Singh, B Khandelwal, “Investigation on elastomer behaviour when exposed to conventional and sustainable aviation fuels” The Aeronautical Journal. (2024)