Paul Puzinauskas
Associate Professor
Department of Mechanical Engineering
Dr. Paulius V. Puzinauskas – College of Engineering (ua.edu)
https://scholar.google.com/citations?user=vOL5ASoAAAAJ&hl=en
Joshua Bittle
Associate Professor
Department of Mechanical Engineering
Associate Director – Center for Advanced Vehicle Technologies
https://jbittle.people.ua.edu
https://scholar.google.com/citations?user=dEM8ysoAAAAJ&hl=en
Ajay K Agrawal
Robert F. Barfield Endowed Professor
Department of Mechanical Engineering
https://scholar.google.com/citations?hl=en&user=IogAX3cAAAAJ
https://Agrawal.people.ua.edu
Students: Wyatt Lassiter, Elliot Johnson, Matt Lundberg, Nik Collins, Rodney Pinder, James Cook
The laboratory focuses on engine and vehicle analysis and testing to support product development. Work in this laboratory often builds upon the early-stage research conducted in High Pressure Spray, Single Cylinder Engines, and Heavy-Duty Engines labs. Engines & Vehicles lab houses multiple single and multi-cylinder engines, a high-performance AC engine dynamometer, and a chassis dynamometer for full-vehicle testing.
Temperature and humidity-controlled air can be ported from the lab’s ‘high bay’ directly into the engine intake system. The test cell is capable of testing vehicles at cold conditions using temperature-controlled fresh air to maintain ambient at close to freezing temperatures. Ventilation and combustion air supply rates are maintained to ensure operational safety and test repeatability. The test-cell has large capacity liquid diesel and gasoline tanks and continuous natural gas supply plumbed in to facilitate long duration testing. The laboratory is equipped with a light-duty dilution system compatible with the ECL’s five-gas emission bench.
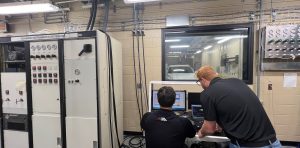
Vehicle Testing. Full vehicle tests are performed on a 600 HP EPA certification capable four-wheel drive chassis dynamometer. This is a two-roller EPA-certification capable (48-inch rollers) AC-powered dynamometer able to measure power output of front, rear, or four-wheel-drive vehicles up to 14,000 pounds gross vehicle weight and up to 350 continuous hp per axle. The system’s rated for 110 [mph] continuous testing speed. The AC systems can be overloaded by 50% for up to one minute, giving a peak capacity of over 1000 HP. Drive-cycles to emulate the desired road conditions can be programmed into standard or customized control systems.
This asset has been used extensively both for funded development programs and by our automotive student design team. An effort is currently underway to physically validate a simulation-based investigation comparing vehicle-to-infrastructure (V2I) application strategies to minimize travel time and fuel consumption. The original investigation was initiated by UA’s EcoCAR team and compares the simulated performance of three different autonomous navigation systems to a simulated human driver in two simulated connected corridors. The three navigation strategies investigated where a V2I-informed constant acceleration kinematic controller (V2I-K), a V2I-informed model predictive controller (V2I-MPC), and a V2I-informed reinforcement learning (V2I-RL) agent. The results showed that the MPC provided most fuel-efficient operation, while the RL agent had the lowest travel times. While the results of this investigation where informative, many physical characteristics of actual vehicle operation are not accurately represented in the system simulation. In particular, efficiency degradation in transient conditions become very difficult to model, particularly with thermal dynamics associate with engine stop-start systems. The physical testing will help characterize these degradations and our fast-response emissions measurement equipment will be employed to quantify the associated emission implications.
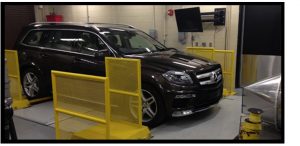
Engine Testing. Lab houses a high-performance AC engine dynamometer. This high-speed unit has a continuous constant torque rating of 470 lb-ft from 0-5000 RPM and continuous constant power rating of 450 HP from 5000-8000 RPM with the power capacity linearly decreasing to 425 at 9000 RPM. The AC system can be overloaded by 50% for up to one minute, giving it a peak capacity of 675 HP.
This equipment has most recently been utilized for examining how water- either combined in hydrous fuel mixtures or separately added- affects the emissions and efficiency at low to medium loads. Water injection has long been used for knock suppression in high-performance engines, but has more recently been investigated for its ability to suppress NOx formation facilitated by water’s high heat of vaporization. The ability to tolerate, or even take advantage of, water content in hydrous fuel mixtures has the potential to significantly reduce the energy required to purify distillate fuels such as ethanol. Generally, the allowable water content is limited by combustion stability degradation and UHC increases. Our work has shown engine out NOx decreases up to 40% under stoichiometric conditions with water content equal to 25% of the fuel. More significantly, similar reductions were found to compound the reductions typical of lean conditions. Our efforts included HC speciation data gathered using our FTIR emission analysis equipment, which showed that high ethanol content fuels UHC levels were most impacted by water dilution; however, a large percentage of this increase was unreacted ethanol. This may suggest ignition enhancement or blending in reactivity improving additives may lead to UHC reduction.
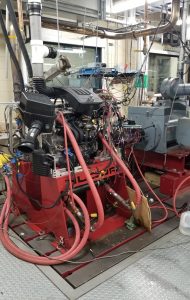
Peripheral Fuel Injection. For heavy-duty on-road diesel vehicles, the environmental protection agency (EPA) has decreased allowable limits for nitric oxides (NOx) by 99.5%, particulate matter (PM) by 90%, and hydrocarbons (HC) by 89% since 1998. Presently, elaborate after-treatment systems are necessary to reduce diesel emissions to within acceptable levels. We have developed Peripheral Fuel Injection or PeFI, a novel fuel injection technique to overcome inherent limitations and drawbacks of Convention Diesel Combustion (CDC) utilized almost universally in existing diesel engines. In PeFI, fuel is injected inwards from the cylinder periphery by multiple single-hole injectors as opposed to CDC whereby fuel is injected outwards from a single multi-hole injector. PeFI eliminates jet/flame wall interactions and thus, reduces PM emissions and coolant heat loss while increasing the thermal efficiency.
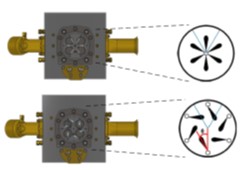
As shown in the figure, we have modified a Caterpillar 3401 single cylinder research engine to operate on the PeFI technique. Test results show significant reductions in engine-out PM and CO emissions, reduced coolant heat loss, and higher thermal efficiency when comparing PeFI and CDC at the same test conditions. We are applying the PeFI technique to simultaneously reduce NOx emissions, noise, and vibration while further improving the fuel efficiency.
Research Examples:
Related Publications:
- Voris, A., Lundberg, M., and Puzinauskas, P., Effect of Ethanol Content, Water Injection, and Compression Ratio on Combustion and Detailed Emissions in an SI-GDI engine, Submitted to Fuels- under revision, 2024-04
- Edward F. Bogdanowicz, Allen Loper, Joshua Bittle, and Ajay K. Agrawal, 2024, “Numerical Investigation of Peripheral Fuel Injection to Increase Performance in Diesel Engines,” FUEL
- Edward F. Bogdanowicz, Allen Loper, Joshua Bittle, and Ajay K. Agrawal, 2024, “Experimental Study of Peripheral Fuel Injection for Higher Performance in Diesel Engines,” International Journal for Engine Research, p.14680874241232007.
- King, B., Olson, J., Hamilton, K., Fitzpatrick, B., Yoon, H. Puzinauskas, P., A Comparative Study of Longitudinal Vehicle Control Systems in Vehicle-to-Infrastructure Connected Corridor, SAE Int. J. of CAV 6(4):2023.
- Voris, A., Lundberg, M., and Puzinauskas, P., “Comparison of Water Dilution Effects on Spark-Ignition Engine Performance and Emissions using Hydrous Fuel Blends and Discrete Water Injection,” SAE Technical Paper 2023-01-0252, 2023.