Ajay K Agrawal
Robert F. Barfield Endowed Professor, Department of Mechanical Engineering
https://scholar.google.com/citations?hl=en&user=IogAX3cAAAAJ
https://Agrawal.people.ua.edu
Joshua Bittle
Associate Professor and Associate Director of Center for Advanced Vehicle Technologies
Sundar Rajan Krishnan
Professor and Associate Department Head for Graduate Studies
Kalyan Kumar Srinivasan
Professor and Interim Department Head
Staff: Mehmet Celik
Students: Yamini Baskara Babu, Kayla Bell, Zac Harris, Muhannad Hendy, Joseph Semler, Mehmet Cellek
Our dedicated High-Performance Computing (HPC) Cluster “Firepower” consists of 14 compute nodes, each with 48 AMD EPYC 7402 2.8GHz 128MB cache processors (totaling 672 processors) with 512GB DDR4 RAM. Six independent LINUX workstations serve as visualization nodes. University maintains academic licenses for computational fluid dynamics (CFD) software including CONVERGE and ANSYS FLUENT. Results from HPC simulations are visualized using Tecplot 360Ex and in-house Python scripts.
High-fidelity CFD simulations are performed to study thermo-fluid processes of internal combustion engines (without or with moving boundaries), rotating detonation combustion, and fuel-air mixing at supercritical conditions. Thermodynamic models and system-level simulations, for example by GT Suite software, are used to obtain zero-dimensional, time-resolved results but with the flexibility to perform parametric studies rapidly.
Engine CFD utilizes CONVERGE CFD software, taking advantage of available models for spray breakup, droplet dynamics, chemical kinetics, turbulence, etc. Typically, we perform Reynolds-averaged Navier-Stokes (RANS) simulations to reduce the computational time otherwise required for large eddy simulations (LES). Depending upon the application, the computational domain can be a constant volume combustion chamber or a piston-cylinder arrangement with moving boundaries. Simulations provide fundamental understanding of jet evolution, autoignition, combustion, soot and NOx formation, and heat transfer processes.
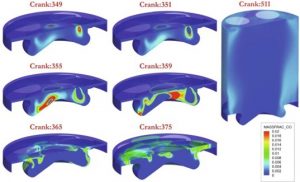
Spray boundary iso-surfaces colored by temperature contours at 1.0, 1,5, and 2 ms aSOI; a-c) Conventional diesel combustion, and Peripheral fuel injection d-f) at 15 degrees, and g-i) PeFI-37.5.
Rotating Detonation. We have introduced the concept of Rapid-to-Gradual (RTG) nozzle to integrate with the rotating detonation combustor (RDC). In our experimental studies, the RTG nozzle has been shown to provide superior performance compared to conventional nozzles for RDC applications.
- Bell, K., Schwer, D. and Agrawal, A.K., 2023. Profiling cross-sectional area of a radial rotating detonation combustor to increase pressure gain. Aerospace Science and Technology, 133, p.108096.
Recently, we have developed a CFD model of radial RDC (RRDC) to complement the ongoing experimental studies in the Gas Turbine Combustion Lab. This realistic 3D model includes complex geometric features such as inlet ports, fuel and oxidizer plenums and associated injectors, radially inwards detonation/combustion channel, aerospike, cowl, and ambient plenum. The model inherently replicates the transient fuel/oxidizer injection processes, fuel-air mixing, rotating detonation, oblique shock wave, supersonic/subsonic flow mixing in the combustion channel until throat, and thereafter, expansion over the aerospike.
Supercritical Mixing. Advanced engine designs and alternative fuels introduce the possibility of supercritical fuel injection in aviation gas turbines and diesel engines, as is already the case for many rocket engines. We have developed high-fidelity CFD models to analyze flows within the injector and fuel-air mixing after injection, both at supercritical conditions. Absence of surface tension in a purely supercritical regime will eliminate the two-phase spray processes, and hence, the timescale for fuel-air mixing can be reduced substantially. Improved fuel-air mixing can be expected to decrease the formation of pollutants in the subsequent combustion process.
- Harris, Zack, Bittle, J., and Agrawal, A.K., 2023, “Fuel Injector Requirements to Achieve Supercritical Flow at the Exit,” AIAA Journal of Propulsion and Power, 40(2), pp.220-232.
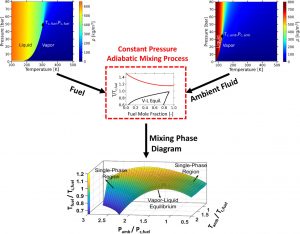
Thermodynamic Modeling. Thermodynamic models and system-level simulations provide zero-dimensional, time-resolved results but with the flexibility to perform parametric studies rapidly. We have developed and validated a multi-zone thermodynamic model of conventional diesel combustion and advanced dual fuel low temperature combustion. It has built-in sub-models to account for fuel injection, fuel evaporation, fuel-air mixing, ignition, spray combustion, premixed turbulent flame propagation (if invoked), and performance and emissions characterization. Recently, we have added ability to perform second law analysis and/or exergy analysis to identify and mitigate thermodynamic irreversibilities in engine processes.
Parallel efforts have included the development of system-level simulations of engine systems (including single-cylinder research engines and production multi-cylinder engines) using GT-Suite software. These system-level simulations have been leveraged to help design a cam-phaser-based variable valve actuation system for a heavy-duty single-cylinder research engine and to guide the selection and matching of a turbocharger to a multi-cylinder medium duty engine.
Research Examples:
Related Publications:
Journal:
- Edward F. Bogdanowicz, Allen Loper, Joshua Bittle, and Ajay K. Agrawal, 2024, “Numerical Investigation of Peripheral Fuel Injection to Increase Performance in Diesel Engines,” FUEL, 371, p.131895.
- Harris, Zack, Bittle, J., and Agrawal, A.K., 2023, “Fuel Injector Requirements to Achieve Supercritical Flow at the Exit,” AIAA Journal of Propulsion and Power, 40(2), pp.220-232.
- Wanstall, C.T., Bittle, J.A. and Agrawal, A.K., 2023. Phase diagram to demarcate supercritical, transcritical, and continuous phase regimes for binary fluid equilibrium mixing relevant to combustion applications. The Journal of Supercritical Fluids, 199, p.105935.
- Bell, K., Schwer, D. and Agrawal, A.K., 2023. Profiling cross-sectional area of a radial rotating detonation combustor to increase pressure gain. Aerospace Science and Technology, 133, p.108096.
- Wanstall, C.T., Bittle, J.A. and Agrawal, A.K., 2022, Transient mixing behavior of a supercritical fluid injected into supercritical and subcritical environments, Physics of Fluids, 34(2), p.023104.
- Harris, Z., Bittle, J. and Agrawal, A., 2022, Role of Inlet Boundary Conditions on Fuel-Air Mixing at Supercritical Conditions. Journal of Energy Resources Technology, 144(6), p.062302.